Contract Manufacturing - Metal Fabrication Services
Metal Fabrication Overview
Every industry relies on metal fabrication. From consumer goods to specialty construction equipment, metal fabrication is used around the world for most commercial and industrial projects.
At New Standard, we serve OEMs by providing contract manufacturing services, including turnkey metal fabrication services. We provide services from initial design for manufacturability and engineering to prototypes to large-scale manufacturing. Our vast customer base agrees that both design and development differentiate New Standard within the marketplace. A few of the industries we work with include:
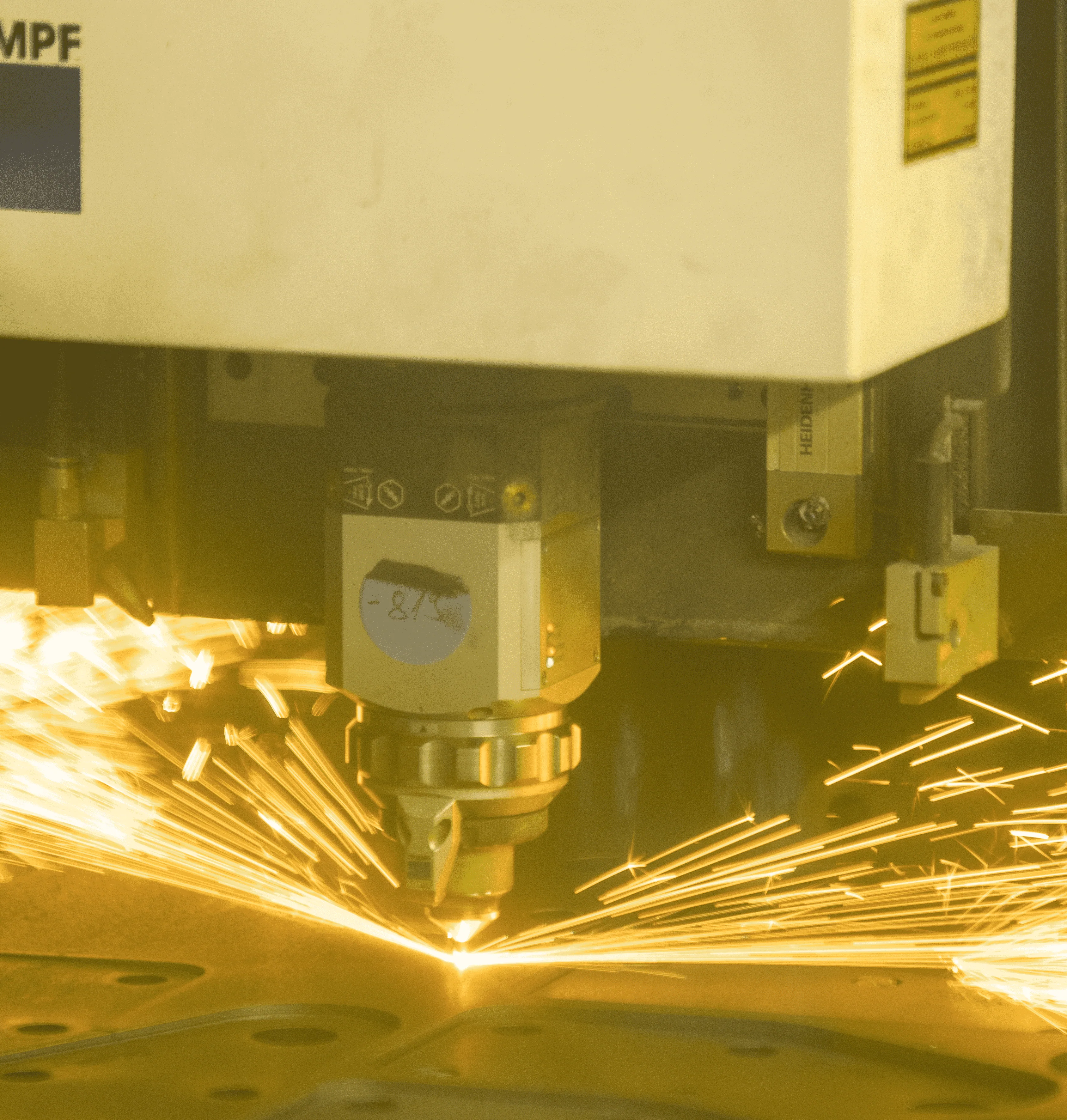
Learn more about our metal fabrication capabilities and how to choose the best contract manufacturer for your project.
Ready To Start Your Next Project?
Key Capabilities in Metal Fabrication
Metal fabrication is the process of forming metal sheets into two- or three-dimensional products and components. The results can be simple or intricate, and modern fabrication tools can create high-quality, extremely precise products. Three of the most common fabrication processes we use at New Standard include press brakes, laser cutting, and welding:
- Press Brakes: Press brakes shape the metal into V- or U-shaped bends or angles up to 120 degrees. Depending on the design of the product, it can include multiple bends at different orientations to create the final form.
- Laser Cutting: Laser cutting uses a powerful, focused laser to cut through the metal workpiece. This precise, energy-efficient fabrication process produces intricate designs with minimal material waste and reduced costs.
- Welding: Welding uses heat and pressure to join two metal workpieces together. New Standard’s experienced welders create precise, reliable welds using metal inert gas (MIG) welding, tungsten inert gas (TIG) welding, and other specialized welding techniques.
New Standard’s fabrication technology offers a solid foundation of mechanical press brakes, CNC punch presses, laser cutters, and manual and robotic welding equipment. At New Standard, we are able to work with cold-rolled steel, hot-rolled steel, stainless steel, galvanized steel, high-strength low-alloy steel, and aluminum. Our vast equipment inventory enables our engineers to support production needs from prototypes to continuous high-volume production.
The Fabrication Process: From Design to Production
High-quality metal fabrication processes follow a clear step-by-step process. Our basic procedure includes these steps:
- Design For Manufacturability: During the design and development stage, our engineers perform fundamental engineering analysis to validate designs and verify performance requirements, making sure the design is ready for full production.
- Cutting Blanks From Larger Sheets: Once the design is ready, we process larger blanks of sheet metal into appropriately sized blanks.
- Bending: Bending tools reshape the metal in a specific sequence to transform the metal into its final form.
- Welding: The welding process joins two metal workpieces together using heat and pressure.
- Finishing: Once formed, parts are finished with paints, coatings, polish, or other finishes to prepare them for delivery or assembly. In assembly, the metal parts are connected with fasteners to form the final product.
- Inspections and Quality Control Processes: Once all the stages are complete, parts are internally inspected for quality. Defective parts can be repaired or recycled. Approved parts are packaged and distributed.
While a traditional fabrication company is pre-disposed to the fabrication process, New Standard considers the total process. At New Standard, we perform thorough quality assurance processes throughout every production cycle to ensure quality and minimize scrap. Close collaboration with customers is crucial to our strengths in design for manufacturability (DFM), optimizing a product’s design for cost improvement, best fit, and proper function. Our process is scalable, allowing us to fulfill large production runs in short time periods.
Case Studies
Oil Coolers
Learn how New Standard’s vertical integration and supply chain expertise helped an OEM increase output and quality for their oil coolers.
Crossmembers
Learn how New Standard helped a customer overcome previous supply chain issues to produce high-quality steel crossmembers for their Class 8 trucks.
Fuel Dispenser Frames
New Standard provides diverse industries with optimized product solutions focused on design and cost improvement. Learn how we partnered with a long-time customer to develop new fuel dispenser frames.
Get Started With Your Contract Manufacturing Partner
New Standard is a contract manufacturing leader in comprehensive metal fabrication and engineering services for OEMs in the agriculture, mining, construction, HVAC, packaging, and other industries. By partnering with our company, you gain access to over a century of experience and a team committed to exceptional quality, efficiency, affordability, and customer service. Contact us today to discuss your application and how we can help.